Das Klinker- und Ziegelwerk in Großräschen - Erinnerung an eine längst vergangene Zeit
Lange Jahre hindurch hatte die Herstellung von Klinkern in Großräschen Tradition. Das Klinker- und Ziegelwerk Großräschen umfaßte mehrere Werke in einem recht weiten Umkreis. So z. B. das Werk I in Großräschen selbst und das ebenso alte Werk in Calau, aber auch das damals bereits sehr moderne und heute noch existierende Werk in Buchwäldchen. Bereits Ende des 19. Jahrhunderts gab es die ersten industriell arbeitenden Ziegeleien, und in einigen schien die Zeit beinahe stehengeblieben zu sein. Wie z. B. in Calau, wo statt der Riemen zur (sogar noch durch das Werk laufenden Transmissionswelle) elektrische Einzelantriebe die Maschinen antrieben und sogar die Dampfmaschine noch gut erhalten stand.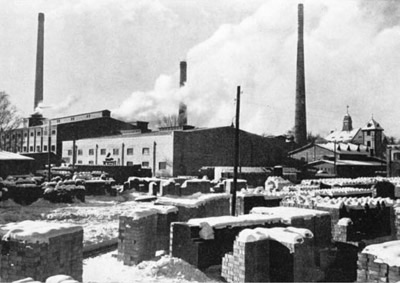
hinten links das Ofengebäude mit den zwei Trockenböden darüber, davor die Sortierhalle.
Außerdem gab es auch noch ein zweites Ziegelwerk in Großräschen, das Werk II in der Straße der Jugend.
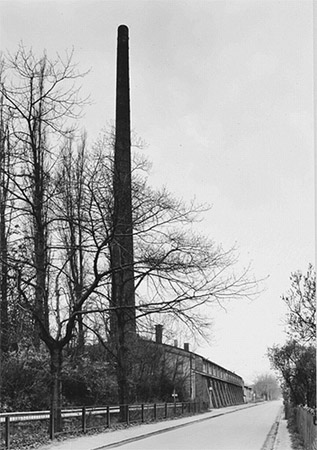
Der gute Ton der Gegend um Großräschen herum war in Verbindung mit der darunter liegenden Braunkohle als billiger Brennstoff eine gute Grundlage für die Ansiedlung der Ziegeleien. Die Tonschicht war teilweise 4 bis 8 m mächtig und lag gemeinsam mit dicken Kies- und Sandschichten über dem 10 bis 20 m mächtigen Kohleflöz. "Zuerst arbeitete ich im Tonberg, also in der Tongrube am Bagger. Da waren kleine Tonmaschinen mit sechs Kippladen. Die wurden vom Bagger beladen und ich musste den Zug einweisen. Wenn die Lore voll war, wurde er vorgefahren, um die nächste Lore beladen zu können. War der beladene Zug fort, war es meine Aufgabe, das Gleis vom Ton, der daneben gefallen war, zu säubern. Erst dann konnte der nächste Zug ranfahren." [1] "Tone und Sande wurden nach bestimmten Qualitätsmerkmalen ausgesucht. Die Ton- und Sandgrube befand sich links der ehemaligen Straße Großräschen-Süd nach Senftenberg" [2]
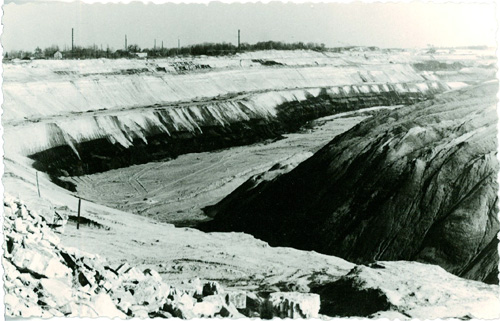
In Werk I wurden sowohl Spaltklinker (auch als Verblender bezeichnet) als auch normalformatige Klinker (1 NF) gefertigt. Die Rohlinge dafür wurden jeweils maschinell, in einer Strangpresse gepresst. Von dort kamen sie mit einer Elevatorkette zur Trocknung auf den über dem Ofen liegenden Trockenboden. Das Einsetzen der Rohlinge auf den Elevator und das Herunternehmen nach dem Trocknen erfolgte von Hand. "Später habe ich auch als Zufahrer gearbeitet. Das hieß, die trockenen Steine vom Niederlass zu den Männern in die Kammer zum Setzen fahren. Es wurde alles über Gleise transportiert. Am Niederlass waren zwei parallele Ketten, an denen es jeweils im Abstand von einem halben Meter eine Schale gab, wo Holzriemchen oben lagen und auf diesen standen die Klinkersteine, die Rohlinge. Wir fuhren mit dem Wagen rein und am Wagen waren Arme dran, die unter die Riemchen mussten. Mit den Beinen wurde ein Hebel bedient, dann ging die Kette los, setzte die Riemchen auf den Wagen, der Wagen wurde gedreht und von der anderen Seite genau so beladen." [1]
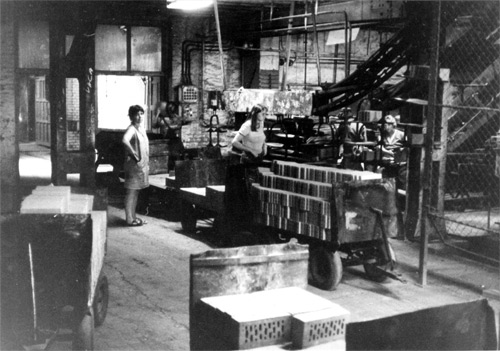
"Später kam ich an die Presse. Die Ziegelei hatte zwei Pressen. Eine Männerpresse, da wurden nur Klinker hergestellt, und eine Frauenpresse. Ich war an der Frauenpresse. Hier wurden Formsteine gepresst sowie Spaltplatten, Spaltläufer, Fußbodenplatten, Klostersteine – eben alles, was man an Formen hatte. Das war nicht leicht. Vor der Presse stand eine Bank, da standen zwei Frauen – eine auf der einen Seite und eine auf der anderen. Die eine nahm die Steine ab und stellte sie auf ein Brett, die andere nahm die Steine und schob sie in die Kette. Wir nannten die Kette den Kreistransportierer. Der Transport ging durch die ganze Ziegelei bis zur Trocknung. Von dort kamen die Steine wieder runter und wir schoben die nächsten rein." [1]
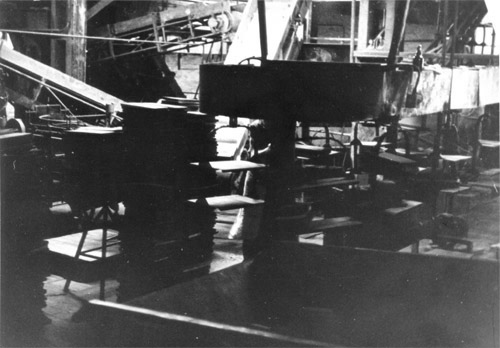
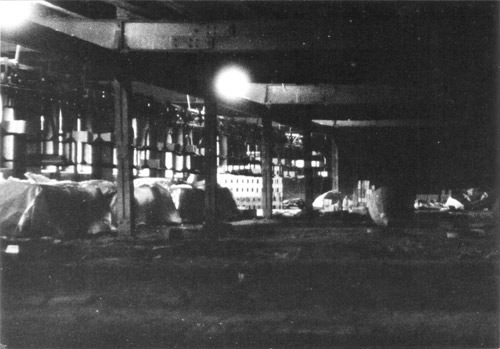
(direkt auf dem Ofen wurde nicht getrocknet, nur seitlich davon).
Außer den maschinell gefertigten Klinkern gab es auch eine Handfertigung. In einer Art Manufaktur wurden Sonderformate gefertig: z. B. Klosterziegel mit z. T. kompliziert geformten Rundungen, wie sie für die Restaurierung historischer Bauwerke benötigt wurden. Und Zierklinker, mit Mustern oder Reliefs. Dazu wurde Ton im Handstrichverfahren in mehrteilige Gipsformen gestrichen und in denen einige Zeit trocknen gelassen, bevor der Rohling aus der Form entfernt werden konnte. Das Herstellen der Gipsformen war ein komplizierter Vorgang, weil dabei das Schwinden der Klinker beim Trocknen und beim Brand bereits berücksichtigt und die Gipsformen entsprechend größer angefertigt werden mußten. "Die gesamte keramische Fertigung lag in den Händen von Hans Streichhan. Er war seinerseits der größte Fachmann, den es im Klinkerwerk Großräschen gab, um diese so schwer zu behandelnden miozänen Braunkohlentone zu verarbeiten. Die Platten sind von Hand gefertigt worden, die Mauerziegel maschinell; ihre Aussortierung erfolgte nach vorgegebenen Farbenmustern. Im Farbton blau/blau-braun/ bunt. Der am längsten dauernde und schwierigste Prozess war die Trocknung der großen keramischen Elemente die eine schwere körperliche Arbeit erforderte." [2]
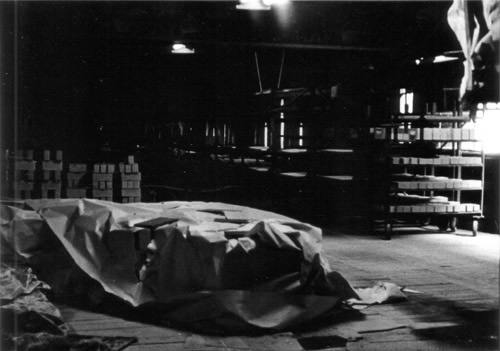
Die Formlinge wurden auf dem Trockenboden von Hand aus den Gondeln der zwischen den Regalen umlaufenden Kette genommen und in die Trockenregale gesetzt bzw. nach der Trocknung mit der Elevatorkette wieder nach unten transportiert.
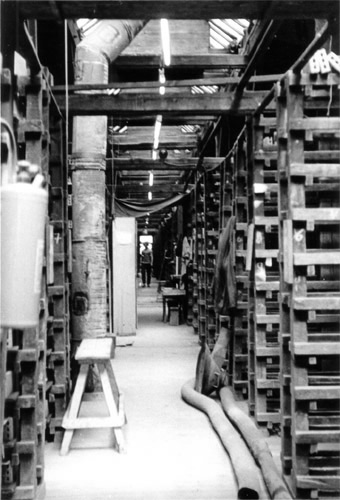
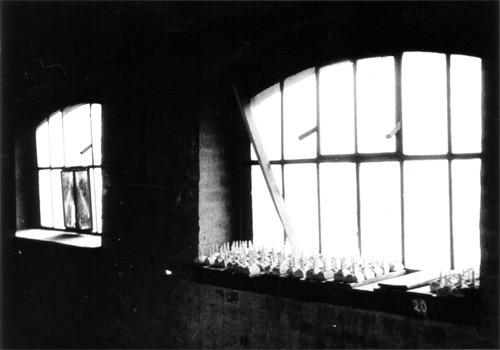
Im Betrieb waren Schienen mit einer Spurweite von 600 mm verlegt, auf denen unter anderem auch die Loren der Grubenbahn rollen konnten. Ansonsten wurden luftbereifte Wagen genutzt, sowohl für Kipploren als auch für die Rohlinge, die zum Setzen transportiert wurden. Diese Wagen wurden von kleinen Dieseltreckern gezogen. "Dann sind wir auf dem Gleis zu den Setzern, über Drehscheiben, in die Kammer gefahren. Es war gefährlich, denn wer nicht das Gleichgewicht ausbalanciert hat, der ist auf der anderen Seite daneben gefahren. Und so ein Wagen wog immerhin zwei bis drei Zentner! In der Ecke stand immer ein Baumstamm, den haben wir vorne drunter geklemmt und wenn wir es alleine nicht schafften, war immer jemand da, der geholfen hat, den Wagen anzuheben. Ja, die Arbeit war schon nicht leicht." [1]
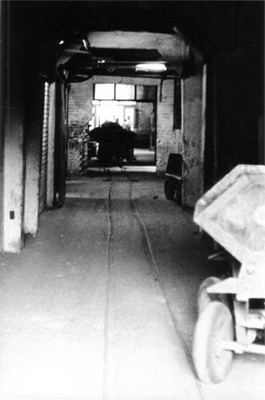
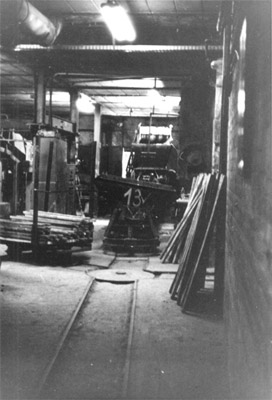
Nach der Trocknung wurden die auf den Latten abgesetzten Rohlinge auf Wagen zum Ofen transportiert und in den Ofen gesetzt. Nach dem Setzen der Rohlinge wurde die Kammer mit Ziegeln und Lehm als Mörtel (um die vermauerungsziegel nach dem Brennen wiederverwenden zu können) verschlossen. Ein 5 cm großes, mit einer Glasscheibe verschlossenes Guckloch blieb an genau der Stelle, wo die Segerkegel in den Ofen gesetzt wurden, um den Brennverlauf beobachten zu können. Der Ringkammerofen in Werk I wurde mit Generatorgas beheizt, das im Werk selbst aus Briketts erzeugt wurde. Vermutlich wegen der Schwefelbestandteile der Kohle war diese Umwandlung ein übelriechender Prozeß. Andere Öfen, in älteren Werken (z. B. in Calau), wurden noch mit Kohle bzw. Briketts befeuert, die durch Feuerlöcher in der Ofendecke hindurch alle viertel oder halbe Stunde in den Ofen geschüttet wurden.
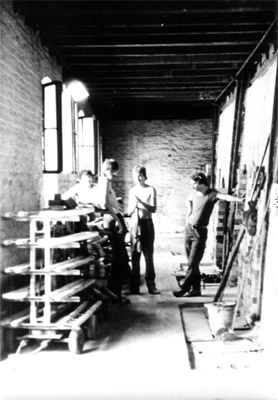
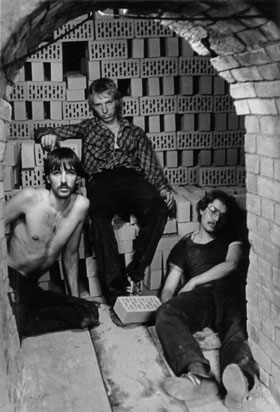
Rechtes Bild: Setzer vor einer fast fertig gesetzten Ofenkammer. In der Mitte des Stapels ist der Hohlraum für die Segerkegel.
Nach dem Brand der Klinker und einer entsprechenden Abkühlzeit (die Külluft wurde dabei sinnvollerweise gleich zum Vorwärmen der nächsten Kammern genutzt) wurden die immer noch recht heißen Klinker aus der Kammer ausgefahren und kamen zur Sortierung und zum Abpacken. "Wir haben die Steine aus den Öfen rausgefahren, wo mein Vorgänger sie rein geschafft hat. Es gab drei große Ringöfen, eine Kammer an der anderen. Da wurden die Steine gebrannt bis auf 1000 Grad Celsius. Wir waren immer in Arbeit! Alles ging damals auf Schienen. Zwei Frauen haben die Loren rausgeschoben, die über die Drehscheiben fuhren. Manchmal sind die Wagen auch von der Drehscheibe gerutscht und es war dann ganz schön schwer, den Wagen wieder einzuheben." [1]
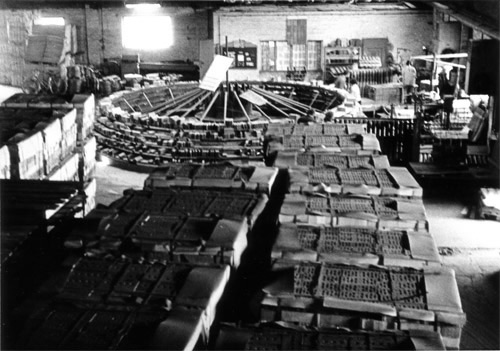
"Die Wagen sind dann von uns raus auf einen Platz gefahren worden, wo Schienen mit einer Drehscheibe in der Mitte gelegt waren. Hier mussten die Steine sortiert werden. Es gab ja x Sorten und wenn nicht für alle Sorten Loren vorhanden waren, wurden die Steine wieder reingefahren und gestapelt. Das war eine mühsame Arbeit. Im Winter haben wir uns mit einem Koksofen die Hände gewärmt, sind in die Kammern gegangen, um zu frühstücken und uns dort aufzuwärmen. Es war alles kalt, den Schnee mussten wir auch immer wegschippen und die Drehscheiben frei machen.
Später wurde eine Halle gebaut. Da war das schon besser, denn dort gab es auch einen Raum, wo wir uns aufhalten konnten, alles war überdacht. In der Halle waren zwei Rampen, da wurden die Pakete gepackt und dann mit Bandeisen zugemacht. 1957 hat die Ziegelei gebrannt und danach wurde ein Ofen weggerissen. Anschließend wurde ein Karussell gebaut. Auch das war dann besser, denn da war sozusagen alles unter Dach und Fach. Vorher war es viel mühsamer. Die Steine, die wir bewältigen mussten, haben ja sechs bis acht Pfund gewogen! Die Vollsteine wurden später abgeschafft und die späteren haben dann bloß noch 6 Pfund gewogen, weil sie Löcher hatten und dadurch leichter waren. Es wurden auch als besondere Rarität Klostersteine von 12 Pfund hergestellt. Die mussten wir dann auch in Stapel packen. Mit dem Leder haben wir die Steine den ganzen Tag über angefasst. Das Leder ging ziemlich schnell kaputt und dann mussten wir neues schneiden, denn ohne Leder konnten wir nicht arbeiten, weil sonst die Finger gleich durch waren.
3.000 Steine haben wir jeden Tag bewältigt." [1]
Zitate aus:
[1] Alles verloren - alles gewonnen? Äußere und innere Landschaften. Eine Spurensuche Ein Theaterprojekt von Jürg Montalta. Großräschen, 2005
[2] Stolz auf die Keramikindustrie. Artikel von Heinz Hager in der Lausitzer Rundschau vom 14.10.2006
Impressum